process parameter in a high pressure die casting process - die casting ppt
by:Hanway
2019-09-01
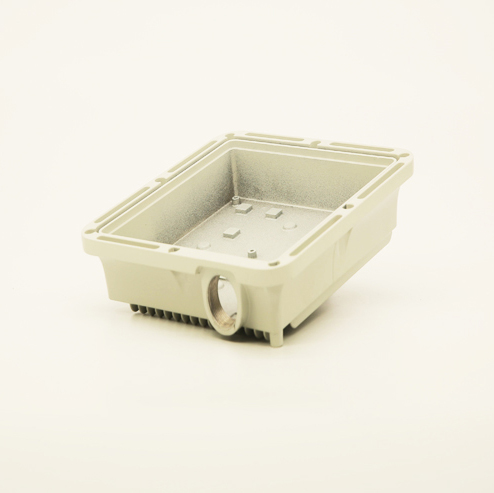
"When the piston moves, we can't do anything anymore," "We can accelerate and slow the piston 5 times during a quick shot," and "When we have good castings, we make temperature images and measure the speed of the piston.
If we have a quality problem, we just have to go back to what we recorded and make the good castings again ".
I heard three statements from a die casting machine supplier and a professor.
What did I learn from it?
All statements have a kernel of truth.
The first scenario is the one we see most in the industry.
The lens is set up and checked by the monitoring system.
Poor casting quality, settings will change, and sometimes parameters will be stored and used for future production operations.
During quick shooting, no parameter changes are used at all.
The key to doing this is to quickly slow down the piston at the end of the shooting to reduce the piston impact load at the end of the filling.
There are several reasons why this opportunity is not used in further details.
The speed reduces the force after melting and does not produce a cold run.
It also increases the filling time, resulting in cold melting and cold running.
The change in the melting volume of the pouring creates a deviation between the switch distance and the melting front.
In other words, we have an unstable process.
So why is the third method not working?
Checking the piston speed is an easy task in many facilities today.
It is much more complicated to measure the temperature.
The camera is very expensive and the mold casters will be shy according to the cost.
The camera is large and therefore cannot capture all areas of interest directly.
The measured value will vary according to the angle.
In order to make the image, production must be stopped and the mold cooled during the capture temperature distribution.
The longer the distance around the machine, the more complex the camera position, the more far away the measured temperature from the real temperature.
It may not be possible to adjust the mold temperature by using water or oil in the passage in the mold.
Cooling the new mold is different from cooling the mold with zoom in the water channel.
The professor told me that the most important thing is the temperature and the piston switch.
Like the timing of the air hole, the gap between the new mold and the components in the old mold changes.
Not to mention keeping the same piston stroke but having a different diameter piston.
Or lay the mold insert flat on its surface in order to find the purpose while reducing the area of the gate.
Now, casting quality and lens parameters change even at the same piston stroke and speed.
As usual, there is no suitable solution for the process parameter set throughout the life of the mold.
As the mold process parameters deteriorate, it may have to be changed.
With more documentation completed and more information on the mold casters, it becomes easier to find optimized machine settings.
Custom message