lost foam casting process - advantages of casting
by:Hanway
2019-09-03
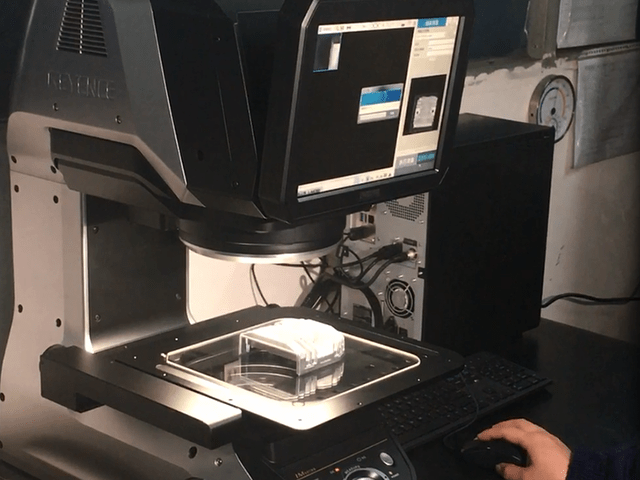
Leakage cost accounting is a sub-type of investment casting.
This casting method uses foam patterns as an investment.
This method benefits from the advantages of foam properties and helps to manufacture simple and cheap castings.
These types of simple castings are not possible using the conventional EDM and drag methods.
Casting process: foam forming: The original foam pattern of polystyrene is usually molded or engraved.
Carved polystyrene: then use a traditional engraving tool or newly carved foam or polystyreneage hot-
Wire cutting tools.
It can also be polished easily.
Injection of polystyrene into the mold: polystyrene contains pentane as a foaming agent and is usually used for beads.
The beads are pre-
Extend, stabilize, and then blow into the mold to form the pattern part.
The steam cycle forces the beads to fully expand, after which the fuse is combined and then it goes through
Mold cooling cycle.
If it is very complicated, the final shape is segmented.
A cluster is formed by aging and bonding the formed foam part.
Prepare the final mold (Investment)
For casting: the gate and riser are usually attached to the pattern and they are also part of the casting as it helps to reduce shrinkage.
Pouring, dipping or spraying is a different method of coating foam clusters with ceramic investment.
The reason for this coating is that it forms a barrier that helps prevent the molten metal from penetrating or causing sand erosion when pouring.
Due to the coating, the structural integrity of the casting is protected.
Cluster in dry with un-backup
Glue the sand and place it in a flask.
Then, proper and even compaction is achieved by using the shaking table for mold compaction.
After all these processes and proper compaction, the mold is ready to be poured.
Automatic pouring is the preferred method for foam casting.
This is the most critical process, which is a little harder than the traditional casting process.
It is easier to remove cleaning because there is no separation line or fins, and it takes less time and operation during foam casting.
Advantages of foam casting: the foam is easy to engrave glue and manipulate due to its unique properties.
It also provides an accurate size because foam casting is more accurate and effective than sand casting.
There is no fin line or parting line. The finishing process is simple and takes less time.
The elimination of the core makes it easy for complex casting designs.
The lost foam casting also allows us to control the wall thickness so that the core print is not required, thus eliminating the shifting or fins and also saving trouble with the defects of the mixed sand and core.
Because there is no draft, multi-level casting can be carried out.
Precise gate and riser replacement is achieved.
Unconventional casting forms, which are difficult or impossible to achieve in the traditional cast and drag methods, are easy to achieve in the calculation of lost foam costs.
Due to the simpler process and easy finishing work, the process is very cost-effective and reduces the overall price of the final product.
Custom message