how does die casting in an aluminum foundry work? - disadvantages of die casting
by:Hanway
2019-08-31
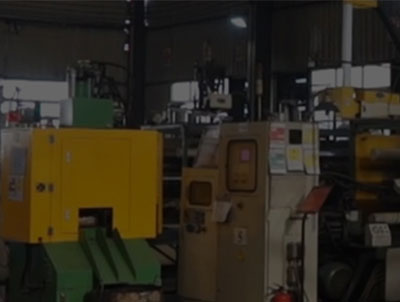
Have you ever thought about some of the most common elements of your favorite everyday items (like cars)are made?
They are usually created in a process called die casting.
"This is a process in which the metal is shaped into the desired shape.
This is quite simple (but intense)
When we use die casting products, it is usually taken for granted.
This process is also called "Metal Casting ".
"Done by forcing liquid metal (
Heat to the metal that becomes the point of melting/fluid)
Enter the mold at extremely high pressure.
The mold is usually made of steel and divided into two pieces.
Their shape and work are comparable to the injection mold.
Most of these die castings are made of metals such as aluminum and zinc.
Because the process is so tight and expensive, it is usually limited to a lot of production.
There are only four main steps in the whole process.
This reduces incremental costs and makes die casting the most suitable for large and medium sized castings.
You can tell by its clean and high quality surface finish that something has been die-cast.
The size of the casting is also very consistent.
Die casting was first invented in Early 1800.
It was originally used in the printing industry but soon helped to grow consumer goods.
It basically makes the production of a large number of complex parts affordable.
There are basically two different types of die casting machines
Hot and cold rooms.
The chamber used during die casting is hot or cold, largely depending on the type of metal used.
The hot chamber machine feeds the mold using a molten/liquid metal pool.
The liquid metal is essentially filled with a "goose neck" after which the piston discharges the metal and pushes it into the mold itself.
It is characterized by fast cycle time (15 per minute)
Convenient.
Unfortunately, metal with very high melting points cannot be used.
These chambers are used with metals such as zinc, tin and lead-based metals.
Cold Room machine when hot room machine can not be used.
Aluminum is die-cast using cold chamber machines.
Other metals used in this machine are magnesium and copper.
However, using a cold chamber die casting machine, the metal needs to melt in a separate furnace. The pre-
The molten metal is then fed into the unheated chamber and driven into the mold via a hydraulic/mechanical device.
The cycle time of the cold room is much slower, plus the pre-
Melt the metal
Usually, two molds are used throughout the process.
These two parts work together, called "cap mold" and "top mold" respectively ".
"The cover mold contains the holes through which the metal flows, while the top-out mold contains pins to allow the casting to be removed from the mold.
The casting is semi-slip out from the cover mold and remains at the top half to ensure that the casting pops up every cycle (
Through the thimble).
Other components include cores and sliders that can generate holes, other details, and weaken the surface.
These other parts tend to increase the cost of the mold.
The four steps of the die casting are: mold preparation, filling, top-out and test mold.
First, the mold is sprayed with a lubricant to help control the temperature and simplify the disassembly of the casting.
Then, under intense pressure, the mold is closed when the molten metal is injected into the mold.
As the casting becomes hard, the pressure in the mold remains the same.
Then open the mold and use the pin to pop up the casting.
Shakeout is where the scrap is separated from the actual casting.
After that, check the casting to make sure everything is OK and the whole process is repeated at a very fast speed (
Especially hot room Machine).
This is how some of your more commonly used items are made.
Custom message