autonomous optimization of uncertainties in the high pressure die casting process - midwest die casting
by:Hanway
2019-08-31
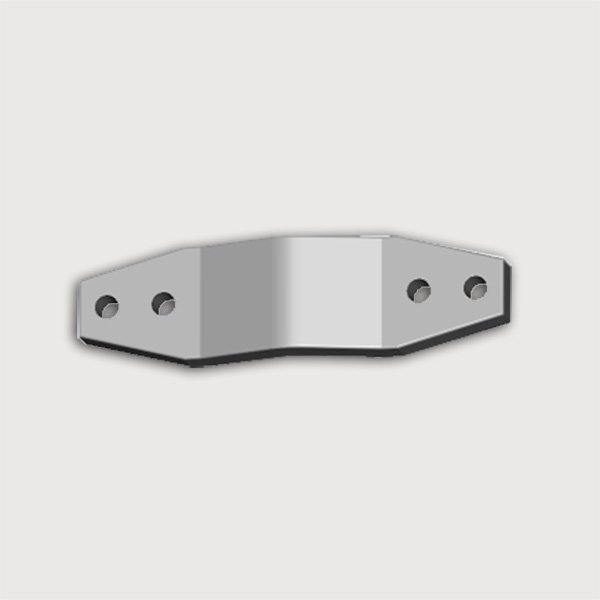
In theory, high pressure die casting process
The pressure die casting process is simple: inject the molten metal into the mold, solidify after a few seconds, and then discharge it as a casting.
The mold is treated with a lubricant to avoid the casting sticking to the mold and then closing at the next "shoot.
In reality, this simple
The vocal process is very unstable.
For example, the nozzle used to spray the lubricant on the surface of the mold may be loose and sprayed in a wider area than expected-
Or may be partially or completely blocked, limiting the amount and area of the spray.
Lack of sufficient lubrication layer, the casting may stick to the mold, cracks appear during the pop-up process, and then must be found and scrapped in the production batch.
Again, the mold keeps the melting volume in the furnace-
The casting machine can change the melting volume quantitatively into the machine chamber.
This in turn changes the metal filling pattern into the cavity by increasing the turbulence and the amount of air accumulated in the casting, resulting in the void.
Or consider a basic variable: the temperature of the mold.
To eliminate pre-
The solidification in the process of filling the mold must make the mold reach an operating temperature of about 400 F/200 °c.
However, the melting of the liquid injected into the mold will heat it to exceed this temperature, and if this temperature is not solved, it will affect the functional life of the mold.
To adjust this variable, the liquid cooling medium containing flowing water or oil is forced to pass through the Channel in the die steel.
Even so, in the production process, the mold itself will change;
When it is heated from room temperature to production temperature, its size increases;
Parts that keep the mold in an unheated state may no longer work properly or completely.
Even in the case of death
During the production cycle, the casting machine itself changes;
When the machine reaches the production temperature, the adjustment made on the cold machine produces a different scale reading.
Changes occur when an unexpected interruption occurs;
The longer the machine stops, the harder it is for the operator to balance the temperature again.
In addition, mold aging will affect the casting results: the mold is worn at different speeds in different areas, which is affected by the flow mode of the melt, the position of the fixture, the proportion
On the cooling line
All of this requires constant efforts by the operator to balance the mold temperature.
All in all, high-
The pressure die casting process is continuous.
The result is in a personal workshop.
It is easy for the process simulation to blame the bad casting on the workshop staff only, because it is unfair.
In most cases, the poor quality is not due to the efforts of the floor personnel, but rather to the earlier stages of the engineering process: the production process may be under-developed;
The casting shape may be poorly designed.
In both cases, high-quality casting will never be achieved.
Here, process simulation can provide the greatest help.
In the first stage of process planning, casting simulation can be carried out long before cutting die steel or releasing the final casting design.
CAD files that simulate the use of early casting design ideas combine theoretical process parameters to point directly to potential problems.
At this point, the casting design and manufacturing process can be changed easily, quickly and cheaply.
With experience, a well
Trained die casting engineers using simulation tools can create processes that produce high-quality castings in the first die casting test.
In most cases, this success is achieved by designing the mold using only one set of possible process parameters.
Given the number of possible parameters present during casting, and the range of variations in these parameters, the number of potential interactions that an engineer can consider is close to infinite-
The same is true for the time required to study these possibilities.
Limited time and resources
These good castings are realized by single parameter simulation.
Engineers may stop at this point and turn their attention to another project, leaving workshop staff to address any further production changes.
Autonomous optimization and uncertain autonomous optimization are mainly used to find a good set of processes, but the dependencies and sensitivity between these process parameters can also be easily identified;
For example, casting and cavity design, filling and cycle times, mold and melting temperatures, and their degree of variation can be defined and simulated in the program.
Optimize the software to independently select parameters, simulate the settings, and evaluate the results.
Through intelligent selection based on genetic algorithms, one of the best parameter sets will be found from thousands of possible variations.
Autonomous optimization should not simulate all possibilities and define "best ";
On the contrary, the goal is to find the best analog quantity in the shortest time
No more than two hours of engineer required (
Set up an hour and analyze the results for an hour. )
Since the simulation is carried out on the office computer and will not affect production, engineers can continue to work on other projects at the same time.
In addition, since the parameter set will not be lost after the simulation is completed, it is also possible to further analyze the parameter set at a later time and analyze the sensitivity of the parameter set to each other in more detail.
In order to start optimization, parameter values are selected either randomly or based on experimental design.
Doing so should provide sufficient results to calculate the sensitivity between defining parameters before starting optimization.
Sensitivity analysis is a by-product
Product of independent optimization;
Using a small experimental design, you can add and analyze this starting array yourself.
Producing good castings in a stable process is an achievable goal;
However, it should not rule out the possibility of further improvement.
It is true that it is very difficult to find uncertainty under production conditions, not to mention to obtain the consent of management to stop production in order to find uncertainty that may not exist at all.
However, the goal that is almost impossible to achieve in the workshop may be a simple goal of the simulation tool.
For example, controlling a single variable in the workshop, such as mold temperature, may be feasible if it is difficult
However, it may not be practical to try to change the mold by welding and grinding in working conditions.
Each change takes time and personnel, and the cumulative effect of welding and grinding reduces the life of the mold so much that this experiment does not make much sense.
However, using computers to simulate these changes, engineers can analyze the efficacy without threatening the life of the mold.
Instead of actually welding the mold, the CAD file is automatically replaced and the selection of the temperature distribution is done by pressing the button.
The use of simulation software is also more effective than the "real world" experiment;
Even if the production of other castings continues, a set of parameters can be analyzed by simulation instead of closing the production line for "trial and error" experiments to produce higher quality castings.
Nevertheless, engineers should consider the time frame involved and the availability of computer hardware and select the most important variables.
Considering the tasks faced by the engineer, he would like to optimize the casting process by considering the following variables: the mold temperature range gives five variation levels from 250 F and 450 F in 50 F increments;
Three levels used to lubricate the nozzle;
Pouring temperature level 4;
The pouring volume is 3, the design of different castings is 2, and the number of simulated iterations is 360.
Depending on the casting design and the use of standard desktop computers, it may take an hour for a simulation;
It can take 15 days to process all 360 permutations
Much faster than trying to do this on a production machine, as long as this check is possible.
With a more powerful computer, this advantage is more likely to be simulated.
Do not extend the release of faster machines in the future.
Even today, through high investment
The calculations discussed can be completed in less than 3 days.
Summing up the use of state-of-the-art computer hardware and correct simulation programs, engineers can provide more about their high
Even before the process development, the pressure die casting process completely ignores the simulation than during production.
Prior to the implementation of manufacturing, processes can be optimized, influencing parameters can be found, dependencies defined, and tolerances can be achieved based on these dependencies and changes in influencing parameters.
With this knowledge and the correct monitoring system, the production process is well understood and can produce good castings in stable conditions.
Custom message