autonomous design and process optimization of a high pressure die casting table base - disadvantages of die casting
by:Hanway
2019-08-31
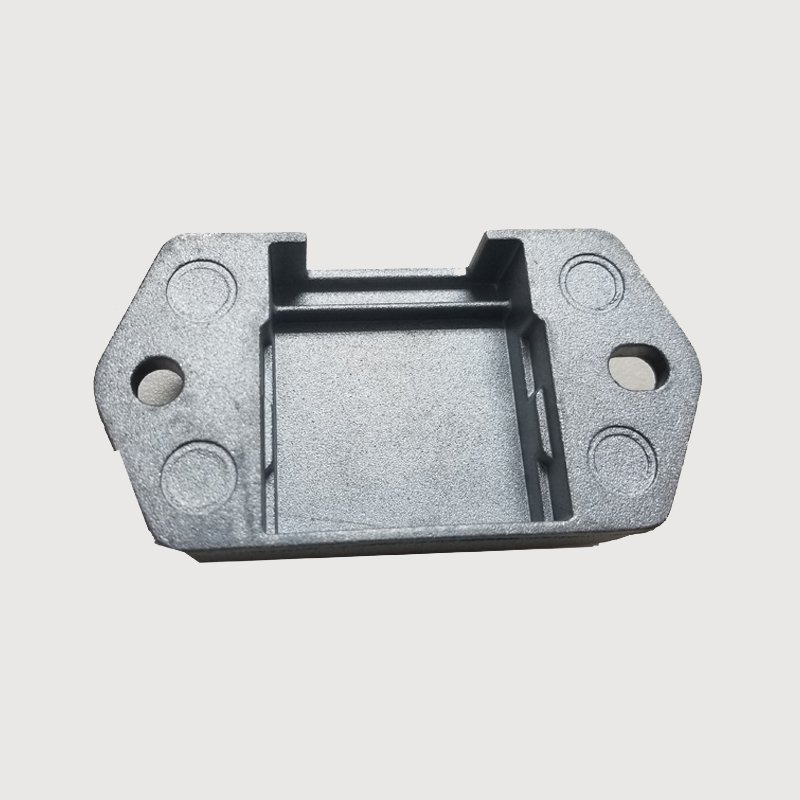
Casting functions and challenges a die casting company and its global partners in Illinois face a challenge: to design and manufacture a die casting tool to produce a large die cast aluminum table base.
The design of the part is complicated because the table has a large bell shape at both ends, smoothly transitioning to a very slender tubular shape at the center of the casting.
Structural integrity throughout the casting process is essential to meet the functionality of the final product, which supports heavy duty desktops, some of which are made of marble.
By heating the casting to a temperature of more than 350 degrees Fahrenheit, a high-gloss coating can be applied.
When the desired temperature is reached, the casting is quickly submerged and stored in the barrel of the special powder paint until the paint in direct contact with the heated casting is liquefied and adhered to it.
The casting is then removed from the powder coating bucket, cooled in water, and the painted surface is solidified.
Any pores close to the surface can spread blisters when heating cycles and/or casting is held in the high temperature of the paint bucket.
Due to the properties of the powder coating, it is not economical to peel off the casting once it is bubbling.
Therefore, it is most important to prevent air holes in castings.
Purpose: to prevent air holes, reducing the air pressure in the casting is the initial target.
Using this standard only, the result can be achieved by increasing the filling time before the air has time to escape.
However, this increased time will allow for a longer period of contact between the melt and the surface of the mold, and a cold flow may occur;
Since the cold material is not welded together, the structural integrity of the casting cannot be achieved.
To prevent this, at the end of the filling, the minimum melting temperature must remain above the solid line temperature, indicating that the two parameters must be considered as part of the casting process.
Process design is limited when designing this casting process, two main objectives must be defined: A: The layout of the mold as the position of the casting, the casting system, the overflow/vent and the cooling system B: the inherent complexity and interactivity of die casting for process parameters for filling cavities and cooling castings indicate that changing only one of the objectives affects the entire casting process design.
For example, by adding or removing spills, the volume of the metal changes, and the heat that is introduced into the mold changes, the position of the piston from slow acceleration to fast shooting will change with the filling pattern in the cavity.
In most cases, the engineer first defines the process parameters.
He knows the casting volume and estimates the filling time based on the casting size, the cavity filling start and end necessary melting temperature and mold temperature.
Similarly, he knows the size of the die casting machine available, the shooting curve and the piston diameter and pressure of the pouring volume.
Since these process parameters are constant, designers can use computer simulations to help design the remaining components, including a balanced runner system, a placement overflow and a temperature control system.
Once the mold is built, the process becomes "written in stone ".
The success of the project falls on the engineer's shoulders to ensure that the best castings are created from the beginning, so that the mold can produce good castings directly from the beginning of production.
However, the reality is that to make a good mold in the first place, process engineers are required to be highly involved in process development.
Multiple designs must be simulated, the results evaluated, the process parameters affected must be determined, and these changes must be simulated again.
While it takes time for all the steps, identifying and understanding the impact of the impact parameters --
And the result of each change to these parameters-
Very challenging and time
Even using simulation software is time consuming.
With the help of state-of-the-art software, the limitations of its simulation capabilities can be significantly reduced.
With a setting, hundreds of designs can be evaluated, weighted, changed, and optimized without human interference.
The result is to optimize the mold layout and the tolerance band of the corresponding process parameters.
The optimization process based on a given casting design, location, and gate system can change the overflow position, gate extension, and process parameters.
There may be two design combinations for side overflow (
Small or wide)
, 4 for runner extensions (
Left, right, average, non)
And four different locations of overflow.
The process parameters are combined with 3 slow shooting speeds, 5 transition positions into fast shooting, 2 acceleration and 5 different fast shooting speeds.
In general, there are 4800 possible combinations that can be considered as potential optimization designs.
Historically, on a standard workstation, the simulation time for each design is 75 minutes.
If all possible designs are simulated, the process will take 250 days.
There is not so much time in today's fast-paced environment.
Automatic optimization software has been developed to find the best by selecting and improving.
To begin optimization, 20 sequences were randomly selected to construct the first generation.
On this basis, 20 sequences of the next generation are constructed.
The goal is a total of 25 generations or 500 simulations.
The simulation results can be listed according to the design sequence of the simulation, or the scatter plot can be listed according to the selected target.
In our example, the target chosen is the maximum air pressure and the minimum melting temperature.
The examination of the results of the optimization of the surface-based design shows that the five optimal designs of the lowest air pressure still have a melting temperature higher than that of the liquid phase line.
For these five designs, both the selected overflow and the size of the added ingates are not important, but the overflow of the middle part of the casting must be in a precise position.
The results also show that both the piston speed in the slow lens and the acceleration in the fast lens are not as important as the early start of the fast lens.
The trend is a position in the middle of the runner.
For all the selected designs, the fast shooting speed itself is the same, without any change, which is obviously an important process parameter to keep the tide tolerance.
The comparison between fast shooting speed and closed air confirms that the faster the speed, the shorter the time to evacuate the cavity, and the more closed air.
Engineers can choose to increase the area of the vent or use a vacuum.
The results also show that extending the runner on one or both sides does not significantly affect the temperature of air interception or melting.
In this case it is recommended not to extend the runner system and save some re-melt material.
The mold layout and process parameter selection at this time will be to keep the overflow layout and add more ventilation, do not extend the runner system, and take the quick shot transition point and piston speed control as important process parameters.
The simulation set up for all of these designs is no doubt longer than the time of a single simulation, but it is not very obvious.
However, the running takes longer to consider the simulation of 500 designs.
However, keep in mind that the evaluation of 500 designs will be carried out without the intervention of engineers, contrary to the time required for engineers to evaluate the results of a single traditional simulation, make changes, re-run the simulation and compare the results with previous results.
Similarly, production process tolerances can be implemented and checked on a regular basis, and process team assessments are required only to show results in the areas of greatest interest.
In our example, in order to perform multiple simulations, a minimum of effort was made and results were produced that were easy to find the critical values and make adjustments in order for die casting to produce the required table bases. Extra Fine-
The design can be adjusted by transferring the parameters to smaller tolerances and creating another empirical design to further optimize the design.
Based on the process knowledge obtained from the first optimization program, and the parameters to be changed or remain unchanged have been determined, it takes only dozens of iterations to re-run.
The result is a design that can reach the production site faster and more efficiently, reduce costs and improve customer satisfaction.
Custom message