aero engine components manufactured - technical die casting
by:Hanway
2019-08-31
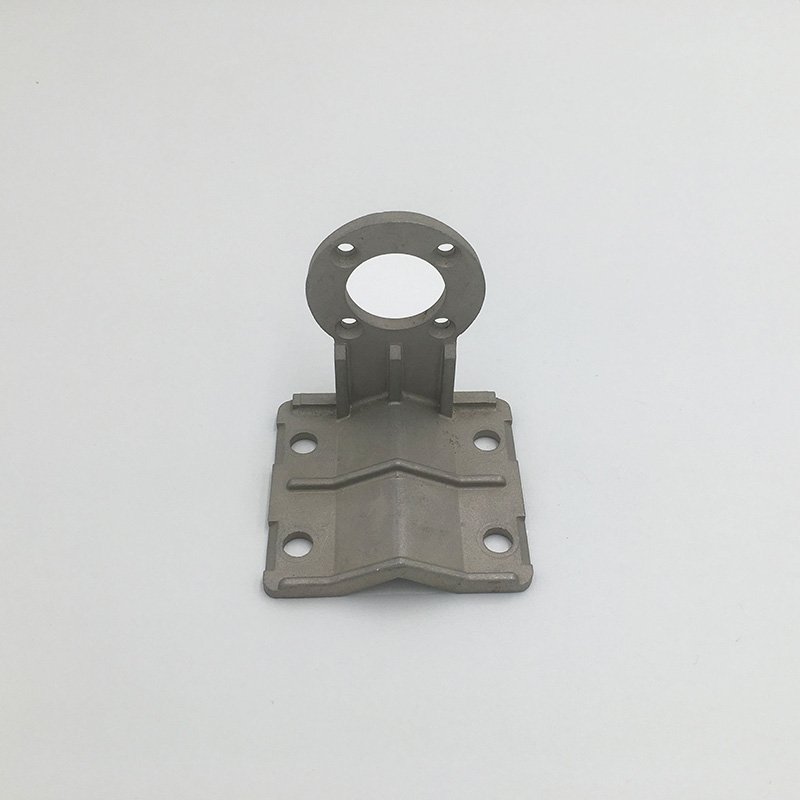
There are a variety of processes used, some for extensive forming of metal parts, some for finishing, others for connecting parts together, and some for changing the condition of the external surface.
Other completely different methods are used to produce parts in the composite.
Aerospace Printing
One of the traditional techniques that people are familiar with is printing, which is used to form part shapes from metal plates.
Especially high.
The strength metal used in gas turbines may have to suppress the material at high temperatures, but even then it is difficult to meet the expected dimensional tolerances.
The metal will distort, bounce back, twist, or otherwise deform, so that it is lengthy (
So expensive)
In order to correct the shape, manual operation may be required, even then it may be lockedin stress.
Better constant temperature (
Constant temperature)
Now, printing is achieved using a heated mold of metal or ceramic, which repeatedly produces precise stressfree shapes.
The hot strike has also achieved good results.
Forming, in which the sheet-
The metal blank is forced into the mold under the feed pressure controlled by the microprocessor to maintain the correct strain-rate.
Ar is one of the inert gases and does not react with metal even in a molten state, thus playing an important role in the manufacture of aero-engines.
Another related process is the ultra-plastic forming SPF.
About 30 years ago, it was found that some metals with proper fine crystal structure could withstand great toughness (tensile)
No tearing deformation.
Through careful control of temperature and strain rate, SPF parts can be manufactured in aluminum, titanium alloy and specific superplastic steel by deep punching.
The press must be specially manufactured, but the molding pressure is quite small.
The finished part can have a very small bending radius and the shape changes so much that the metal actually flows.
For example, the billet can be squeezed into thin
Wall part with integral reinforcement.
SPF is often combined with diffusion connections to produce complex components that are actually a piece of metal, not made by connecting a dozen separate components.
Sheet metal rotation.
Another ancient craft is sheet metal rotation.
The modern equivalent is flow-
The workpiece is usually a flat disk at first (a blank)
Forced by a computer
The control roller is bent around the center rotating mold called the core shaft.
The result is almost any desired cone or even cylindrical shape that fits exactly the size of the no joint.
Previously, this part had to correct the shape by packing and welding the sheet and then drawing and adjusting the dimensions. CNC machining.
Another familiar technology is aerospace cnc machining in which hard tools cut the material off the workpiece.
There are many kinds of CNC machining.
In turning, the part rotates on the lathe while being cut by tools that slowly enter or move along the workpiece.
In CNC milling, it is the work of moving slowly by rotating the tool.
Fixture drilling is a high
Precision Vertical milling.
Broaching includes pulling or pushing the tool from the workpiece to process a straight line slot, such as fir-
The root or flower column along the axis;
A pull knife is a linear tool with many teeth, each close to the finished outline.
All the processing today may be computer numerical control.
The machine tool is controlled by the computer, and the computer inputs the tape that is compatible with the specific part.
This greatly saves time and makes it possible to quickly process complex shapes that may have to be forged, cast or assembled by connecting many parts together before.
It actually eliminates human error as well, so "scrapes" have almost become the past.
Aerospace grinding
There are many other techniques that can be used to shape a part.
In grinding, the cutting is carried out by millions of very hard particles projected from the micro-surface of the wheel or roller.
In electrolytic grinding, the wheel is conductive and immersed in an electrolyte bath with the workpiece (
Conductive liquid, usually a solution of salt).
The rotating wheel does not touch the workpiece much, but removes small particles through an electrochemical reaction.
The rotation of the wheel swept through-
The product that inhibits the reaction.
Aerospace castings and die forgings.
Casting and forging are the highest in the basic forming method.
In heavy engineering, forging refers to heating a rough metal billet or plate to a degree of almost melting, and then squeezing into shape on a large press or through a blow of steampowered hammer.
In the manufacturing of gasturbine, almost all forging is forged, in which the workpiece-
Almost white in some cases.
It's hot in other places at room temperature
Squeeze in the press between the upper and lower molds.
Such as main drive shaft, compressor housing or half
The housing, burner rings, rotor discs, blades and gears can be forged very close to the shape and size of the finished product.
Mold forging is an economical method of producing parts, in the case of blades, combining thin wings with distortion and bending, other methods are difficult to manufacture this except ECM
In constant temperature hot forging, the mold is in a constant temperature furnace.
This precision forging requires precise control of the forging temperature and the absolute cleanliness of the mold.
Forged parts are also called forged parts.
A special type of forging, usually used to make blades, that is, top forging.
The rod material is fed into the machine, the machine takes the working end of the rod material to the forging temperature at high speed, and then, through the hydraulic control of the feed of the stock and the exit speed of the top hammer pressed at the end, make the end of the rod have a specific irregular profile.
The profile is properly distributed in metal to create roots, tips and any shields or shields in subsequent forging.
A process similar to forging is extrusion.
As the name points out, this forms a linear part of a constant cross
Squeeze it through the right shape of the mold like a toothpaste.
It has been used for many engine parts, including rings used to reinforce the housing, which of course need to be bent into a circle and then connected to the end.
Most metals are not difficult to squeeze out, but steel was a challenge 40 years ago before a French company discovered that molten glass could be used as a lubricant.
In casting, the metal is melted and entered into the mold as a liquid.
Therefore, the problem of forming refractory materials (heat-resistant)
The alloy is stepped on the side.
Very hot parts, such as the flap of the rear burner main nozzle, used to be welded from thin sheets, but today it is cheaper to cast into one piece.
Casting is also used to manufacture parts such as aluminum gearbox housing.
In traditional casting, the mold is made of sand, and the pattern is a replica of the part to be made.
In die casting, permanent molds are used.
Centrifugal casting is a special form of casting for the manufacture of circular parts.
The mold here is usually water.
The cooled metal, for faster solidification, rotates at high speed on the vertical axis to obtain a high density finished product without defects.
The most important method for turbine blades is to invest or "lose"wax' casting.
Used by Chinese around 2000 BC, it started to make more than one
The workpiece steel mold containing a highly polished internal cavity with an exact reverse shape of the finished part.
Carefully inject the melted wax to fully fill the mold and allow it to be set up as a replica of the finished part of the production. Several -
Usually from 2 to 20-
These same patterns are then assembled on the "wax door tree" for Christmastree style.
It is then immersed in a liquid ceramic paste that is quickly dried.
The tree is dipped a few more times until the ceramic coating is about 6mm (0. 25 in)thick.
Then the wax melts and runs out, be careful to make sure that each ceramic housing mold is fired at temperatures above 1,000 °c, completely free of waxThe red-
Then fill the hot mold with the blade alloy, the blade alloy is electric
It senses melting and reaches a precise temperature.
After cooling, remove the ceramic housing, cut the blade from the cast gate tree, clean it chemically, and check it carefully through a variety of methods.
Many of the engine's hot segment components are cast in investment casting, but for turbine blades, investment casting is particularly important.
Custom message